To use a plasma cutter, connect it to an air compressor and a power source, then turn it on and guide the torch along the metal to cut. A plasma cutter uses an electrical arc and compressed air to cut through metal quickly and accurately.
With the right setup and technique, a plasma cutter can be an efficient tool for metal cutting projects. Plasma cutters have become popular in recent years as they offer a fast and precise way to cut through metal. These tools use compressed air and an electrical arc to create plasma, which melts and cuts through metal quickly. Plasma cutters can be used for a variety of metal cutting projects, such as fabricating metal parts, repairing automotive parts, or creating metal sculptures. In this guide, we will go over the basic steps to use a plasma cutter safely and effectively. From setting up the cutter to selecting the right settings, we will cover everything you need to know to start cutting metal with ease.
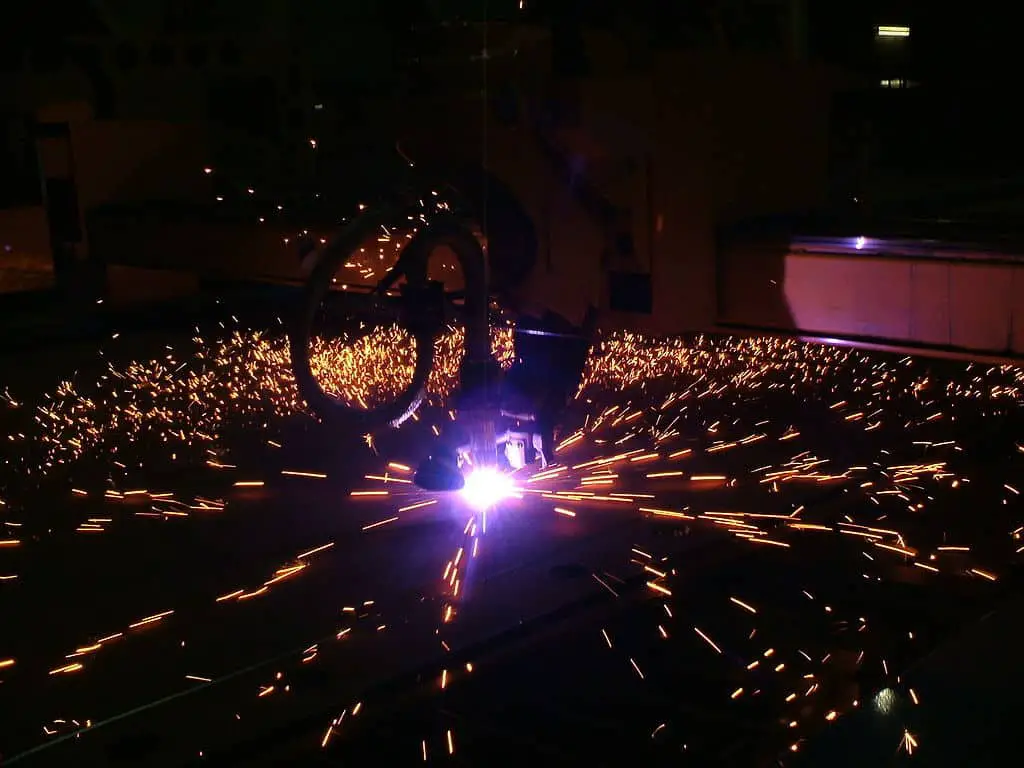
Credit: www.newson6.com
Understanding Plasma Cutting
Table of Contents
Plasma cutting is a popular metal-cutting technique that utilizes ionized gas to create incredibly high temperatures. The technology involved in plasma cutting is fascinating, and understanding the process is essential to use it safely. In this section, we will discuss the basics of plasma cutting, including what it is, the advantages of plasma cutting, and safety precautions to keep in mind while using a plasma cutter.
What Is A Plasma Cutter?
A plasma cutter is a machine that uses plasma to cut metal. The plasma generated by the plasma cutter is contained in a torch, which focuses the plasma down to a fine point to cut through metal. The machine’s power source generates an electrical arc that ionizes the high-velocity gas passing through it, creating the plasma that is used to cut the metal.
How Does Plasma Cutting Work?
Plasma cutting works by superheating gas into a plasma, which can reach temperatures of up to 30,000 degrees fahrenheit. The plasma cutter uses an electrical arc to produce this temperature, ionizing gas, and making it positively charged. The plasma cutter then directs a jet of gas towards the metal you want to cut.
When the plasma stream comes into contact with the metal, it melts the metal, and the gas blast blows away the molten material.
Here are the key steps involved in plasma cutting:
- The plasma cutter generates an electrical arc between the torch and the metal to be cut.
- The arc ionizes gas flowing through the torch, creating plasma.
- The plasma is directed as a high-velocity jet towards the metal, melting it.
- The gas blast blows away the molten metal, cutting through the metal.
Advantages Of Plasma Cutting
Plasma cutting is a versatile and highly efficient method of cutting metals.
- High precision cutting without creating heat-affected zones in the metal
- Ability to cut cleanly through thick metal with ease
- Faster cutting speeds than traditional torches or saws
- Low operating cost and minimal maintenance requirements
- Can cut through a wide range of conductive materials
Safety Precautions To Keep In Mind When Using A Plasma Cutter
Safety is essential when using a plasma cutter, as the equipment can be dangerous if not operated correctly.
- Always wear appropriate safety gear, including gloves, eye protection, and hearing protection.
- Keep the area free of flammable materials and away from combustibles.
- Make sure the plasma cutter is correctly grounded and well-maintained.
- Never touch the metal or the torch while the plasma cutter is running.
- Turn off the power when changing consumables or working on the machine.
- Allow the metal to cool before you handle it, as it will be hot after cutting.
By following these safety guidelines, you can reduce the risk of injury while using a plasma cutter. Always make sure you have received appropriate training and understand the operation of the plasma cutter before use.
Setting Up Your Plasma Cutter
Plasma cutters are versatile and powerful tools that can cut through a wide range of materials with precision and ease. Whether you’re a diy enthusiast or a professional metalworker, a plasma cutter can make your life a lot easier. But before you dive headfirst into using a plasma cutter, it’s important to know how to set it up properly.
This section of the blog post will guide you through the process of setting up your plasma cutter, step by step.
Choosing The Right Plasma Cutter For Your Needs
The first step in setting up your plasma cutter is choosing the right one for your needs.
- The thickness of the materials you’ll be cutting: different plasma cutters have different amperage levels, which determines how thick a material you can cut. Make sure you choose a plasma cutter that can handle the thickness of the materials you’ll be working with.
- The type of materials you’ll be cutting: some plasma cutters are better suited for certain types of materials. For example, a plasma cutter with a high-frequency start may be better for cutting stainless steel, while a drag-start plasma cutter may be better for cutting aluminum.
- Your budget: plasma cutters come in a wide range of prices, and you can easily spend thousands of dollars on one. Make sure you choose a plasma cutter that fits your budget, but still meets your needs.
Necessary Equipment For Plasma Cutting
Before you can start using your plasma cutter, you’ll need to make sure you have all the necessary equipment.
- A plasma cutter: of course, you’ll need a plasma cutter to get started.
- A compressor: plasma cutters require compressed air to operate, so you’ll need to have a compressor or access to one.
- Safety gear: plasma cutting can produce a lot of heat and sparks, so you’ll need to wear safety gear, including a welding helmet, gloves, and protective clothing.
- Consumables: plasma cutters require consumables, including electrodes, nozzles, and shields. Make sure you have plenty of these on hand.
Setting Up Your Workspace
Once you have all the necessary equipment, it’s time to set up your workspace.
- Choose a well-ventilated area: plasma cutting produces fumes and smoke, so you’ll want to choose a well-ventilated area to work in.
- Clear your workspace: make sure your workspace is free of clutter and debris, and that there’s enough room to move around.
- Set up your compressor: make sure your compressor is set up and ready to go, with the correct air pressure and moisture control.
- Connect your plasma cutter: connect your plasma cutter to the compressor and power source, and make sure all the connections are secure.
Preparing Your Materials
Once your workspace is set up, it’s time to prepare your materials.
- Clean your materials: make sure your materials are clean and free of rust, oil, or other contaminants that could affect the quality of your cuts.
- Measure and mark your materials: use a measuring tape and a marker to measure and mark your materials, so you know exactly where to cut.
- Clamp your materials: use clamps or magnets to secure your materials to your work surface, so they don’t move while you’re cutting.
By following these steps, you’ll be well on your way to setting up your plasma cutter and making precise, clean cuts on a wide range of materials. With practice, you’ll become a pro in no time!
Beginners Guide to Plasma Cutting and Plasma Gouging
Basic Plasma Cutting Techniques
Plasma cutting can be a daunting task for beginner welders, but with practice and the right technique, it can be quite simple. Here are some basic plasma cutting techniques to help you get started.
How To Perform A Straight Cut
Performing a straight cut is the most fundamental technique in plasma cutting.
- Ensure that the metal is clean and free from any rust or debris.
- Secure the metal you want to cut onto a flat and stable surface.
- Turn on the plasma cutter and adjust the amperage and air pressure based on the thickness of the metal.
- Hold the plasma torch at a 90-degree angle to the metal, and ignite the plasma arc.
- Steadily cut the metal, ensuring you hold the plasma torch steady and keep it straight.
Tips For Cutting Curves And Circles
Cutting curves and circles with a plasma cutter can be challenging.
- Practice making small cuts first as you get a feel for the plasma cutter’s motion and sensitivity.
- Use a guide to help maintain a smooth curve, such as a straight edge or circle template.
- Try to keep the plasma torch in motion and avoid starting and stopping in one spot.
- Slowly cut the metal while moving the torch in a circular or curved motion.
Piercing Metal And Cutting Holes
Cutting holes in metal can be quite challenging using a traditional sawing method.
- Ensure that the metal is clean and free from any rust or debris.
- Secure the metal you want to cut onto a flat and stable surface.
- Find the perfect spot to pierce through the metal, mark it, and begin the piercing process.
- Once the metal has been pierced, continue cutting as required.
- To create a hole, move the plasma torch in a circular motion.
Cutting Thicker Materials
Cutting thicker metal with a plasma cutter requires the right technique and adjustments.
- Increase the amperage and air pressure on the cutter to provide enough heat and velocity to cut through thicker metals.
- Ensure that the plasma torch is clean, and the electrodes are in good condition.
- Employ a drag technique where you hold the torch at a 15-degree angle and drag it along the metal’s surface.
- Move the plasma cutter slowly and steadily to obtain a smooth cut.
By following these basic plasma cutting techniques, you’ll be able to perform precise cuts with your plasma cutter. Remember always to keep your safety gear on and take precautions when operating the plasma cutter.
Advanced Plasma Cutting Techniques
Plasma cutters are highly versatile and efficient tools for metalworking, offering precise cutting for various applications. Here, we will provide insights into advanced plasma cutting techniques that can help you achieve advanced cuts, precision, and quality.
Bevel Cutting And Chamfering
Bevel cutting and chamfering use specialized nozzles and machining techniques that allow you to achieve angled cuts on metals. You can use these techniques to create joints, produce weld preparations, bevels, and chamfers on metals.
Some useful tips to facilitate bevel cutting and chamfering include:
- Study the thickness, angle, and the bevel’s length before commencing the cut.
- Maintain a consistent speed while cutting to prevent variations in the bevel angle.
- Use a square and a protractor to ensure that you maintain a neat and accurate bevel angle.
- Employ the back cut technique to attain perfect angles on heavy-duty metals.
Marking And Engraving Using A Plasma Cutter
Plasma cutters can also be used for marking and engraving programs to produce intricate designs in metals. By altering the nozzle and controlling the gas flow, you can create precise engravings, logos, serial numbers, and letters in metal.
Some useful tips to facilitate marking and engraving include:
- Use stencils or templates to achieve consistent and replicable marking.
- Use high-quality consumables like nozzles, electrodes, and gas to prevent and reduce slag buildup.
- Dictate kerf width with the tool settings for your desired level of precision and accuracy.
- Clean the engraved surface using a wire brush to remove debris and oxides.
Tips For Cutting Non-Metallic Materials
Plasma cutters can also cut non-metallic materials, including wood, plastics, and carbon fibers. However, cutting non-metallic materials requires specific consumables, settings, and techniques that differ from metal.
Some useful tips to facilitate cutting non-metallic materials with a plasma cutter include:
- Use a straight edge guide to achieve straight and accurate cuts.
- Experiment with the power settings and travel speed to achieve the desired cut quality.
- Use specialized consumable nozzles that can handle non-conductive materials.
- Make sure to wear appropriate ppe since cutting wood, plastic, and carbon fibers with a plasma cutter produces toxic fumes and debris.
Final Thoughts
With advanced plasma cutting techniques and tips, you can improve your metalworking skills and achieve quality cuts and engravings. Plasma cutters are highly versatile and efficient tools that can handle different materials, thicknesses, and designs. Remember always to comply with ppe and manufacturer instructions to ensure a safe working environment.
Troubleshooting And Maintenance
Plasma cutters are an indispensable tool for cutting through metal quickly and precisely. However, like all tools, the plasma cutter may encounter issues with prolonged use and the need for maintenance. In this section, we will focus on some common issues that people face while using plasma cutters and how you can troubleshoot them.
We will also discuss some regular maintenance tips that will help keep your plasma cutter in top shape.
Common Issues And How To Troubleshoot Them
Here are some common issues that you may face while operating your plasma cutter and some simple ways to troubleshoot them:
- No arc or weak arc: check the air pressure, make sure the electrode and nozzle are clean and replace if necessary, and check if the power supply is not faulty.
- Uneven cuts: check if the consumables are in good condition, adjust the cutting speed, and ensure the metal is flat and clean.
- Excessive slag: adjust the cutting speed, ensure the air pressure is optimal, make sure the electrode and nozzle are clean, and replace the consumables if necessary.
- Overheating: check if the fan is running, ensure there is enough space around the plasma cutter for ventilation, and make sure that the air filters are clean.
Regular Maintenance To Keep Your Plasma Cutter In Top Shape
Just like any other tool, proper maintenance is essential to keep your plasma cutter functioning optimally.
- Check the air filters regularly and clean or replace if necessary.
- Change the consumables regularly as instructed by the manufacturer.
- Lubricate the machine’s moving parts, such as the torch height control, on a regular basis.
- Inspect the power cord and other electrical components for any damage.
- Keep the machine and its surroundings clean and free of debris.
- Store the machine in a dry and safe place.
Troubleshooting Your Plasma Cutter’S Consumables
The consumables of a plasma cutter can wear and tear over time and may need periodic replacement.
- Check the nozzle and the electrode for any damages before and after cutting.
- Ensure that the right consumables are used for the specific application.
- Clean the consumables regularly to prevent any slag buildup.
By properly maintaining and troubleshooting your plasma cutter, you can ensure its longevity and optimal performance. Following the above tips can help you keep your plasma cutter in top shape and avoid any unnecessary downtime.
Frequently Asked Questions Of How To Use Plasma Cutter,
What Is A Plasma Cutter And How Does It Work?
A plasma cutter is a tool that uses a plasma torch to cut through various metal materials. The plasma torch creates a high-temperature, high-velocity jet of ionized gas that melts and removes material, resulting in a precise, clean cut. The cutter requires an air compressor to work effectively.
What Safety Precautions Should I Take When Using A Plasma Cutter?
Some important safety precautions to take when using a plasma cutter include wearing appropriate personal protective equipment (ppe), understanding your surroundings, cutting away from yourself and others, avoiding cutting on or near flammable materials, and ensuring proper ventilation in your workspace.
What Materials Can I Cut With A Plasma Cutter?
A plasma cutter can cut through a variety of metal materials, including mild steel, stainless steel, aluminum, brass, and copper. The thickness of the material will affect the speed and efficiency of the cut.
How Can I Maintain My Plasma Cutter?
Regular maintenance of your plasma cutter, such as cleaning the torch and replacing consumable parts, can help ensure it remains in good working condition. Refer to the manufacturer’s instructions for specific maintenance guidelines for your model.
Conclusion
As you have learned, a plasma cutter is a versatile and powerful tool that can make cutting metal a breeze. By following the tips outlined in this guide, you should now be able to safely and effectively use a plasma cutter.
Whether you’re a professional metal worker or a diy enthusiast, investing in a plasma cutter for your metal cutting needs is a wise decision. Remember to take the time to choose the right cutter for your needs, make sure you have all the necessary safety gear, and practice using the tool before taking on big projects.
With these precautions in place, you’ll be able to create precise cuts in metal with ease and efficiency. So go ahead, get started on your next project and unleash your creativity with a plasma cutter!