There are a few different types of lathe tool inserts that can be used with Harbor Freight lathes. The most common type is the indexable insert, which is available in a variety of sizes and shapes. These inserts can be swapped out quickly and easily, making them ideal for use with a variety of different materials.
Other types of inserts include carbide-tipped and high-speed steel (HSS) varieties. Each type has its own advantages and disadvantages, so it’s important to choose the right one for the job at hand.
How to use the HF Carbide Tipped Lathe Tool Set
Table of Contents
If you’re looking for lathe tool inserts, Harbor Freight has a great selection. With a variety of sizes and styles to choose from, you can find the perfect insert for your project. And best of all, they’re very affordable!
Carbide Inserts for Harbor Freight Lathe Tools
If you own a Harbor Freight lathe, you know that the factory-supplied carbide inserts leave something to be desired. They’re made of cheap carbide and they don’t hold up well to repeated use. Fortunately, there are aftermarket options available that can give your Harbor Freight lathe tools a major upgrade.
There are two main types of carbide inserts for Harbor Freight lathes: round and square. Round inserts are more versatile, but square inserts provide more support for cutting operations. Both types are available in various sizes and shapes to suit your specific needs.
Round carbide inserts are held in place with a set screw, while square carbide inserts fit into a machined slot in the tool holder. Changing out the inserts is a simple process that takes just a few minutes.Once you’ve upgraded to better quality carbide inserts, you’ll wonder how you ever got by with the stock ones!
Your cuts will be smoother and more precise, and your tools will last longer too. If you’re serious about woodturning, investing in better quality carbide insert is a no-brainer.
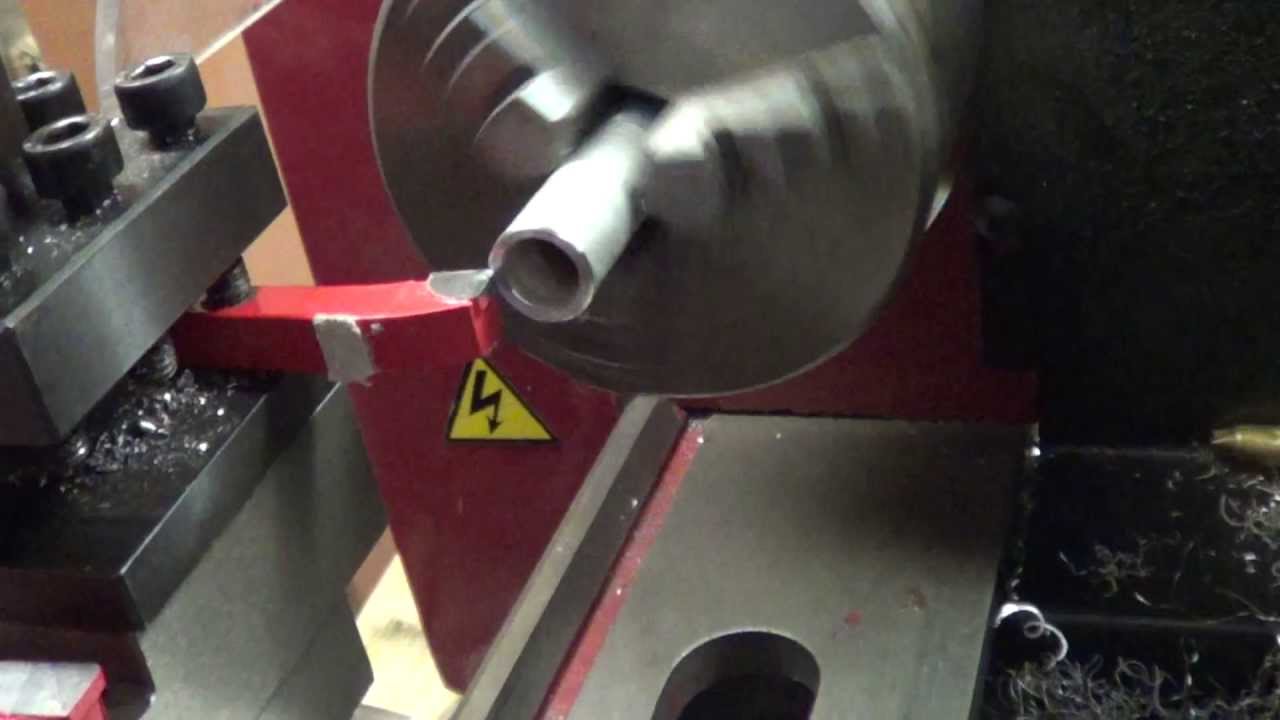
Credit: www.youtube.com
How Do You Mount a Tool on a Lathe?
Assuming you would like a blog post discussing the process of mounting a tool on a lathe:“How do you mount a tool on a lathe?”The first thing you need to do is identify the specific type of tool that you will be using.
There are various types of tools available, each with their own specific purpose. Once you have identified the type of tool, it is time to begin mounting it onto the lathe.The first step is to secure the tool holder onto the spindle nose.
Next, use an arbor or similar device to fix the cutting tool onto the holder. Finally, tighten all screws and clamps to ensure that the tool is firmly in place before beginning your project.With proper care and attention, following these steps will ensure that your cutting tool is mounted correctly and safely onto the lathe.
How Do You Use Carbide Lathe Tools?
Carbide lathe tools are made from tungsten carbide, a material that is harder than high-speed steel. This makes them ideal for machining metals that are difficult to work with, such as stainless steel and cast iron. Carbide tools can also withstand higher temperatures than high-speed steel tools, making them ideal for use in high-speed machining applications.
When using carbide lathe tools, it is important to take care not to overheat the material being machined. Tungsten carbide can lose its hardness if it gets too hot, so it is important to keep cutting speeds low and use coolant when possible. It is also important to use sharpening techniques that preserve the integrity of the tool’s cutting edge.
How Do You Sharpen Brazed Carbide Lathe Tools?
Brazed carbide lathe tools can be sharpened by first removing the existing brazed on tip. This can be done with a variety of methods, but the most common is to use a grinding wheel or an abrasive cutoff wheel. Once the old tip has been removed, a new one can be brazed on in its place.
The new tip should be positioned so that it extends past the edge of the tool body by about 1/16” to 1/8”. Once in position, it should be tack welded in place and then finish welded using a gas tungsten arc welder (GTAW).After the new tip has been welded on, it will need to be ground to the desired shape.
This can be done using a variety of methods, but the most common is to use a grinding wheel or an abrasive cutoff wheel. The cutting edge should be ground at a angle between 10 and 30 degrees relative to the tool axis. The specific angle will depend on what type of material is being machined and what kind of finish is required.
Once the cutting edge has been ground to shape, it will need to be honed using a fine grit abrasive stone. This step is important because it removes any burrs that might have been left behind from grinding and makes sure that the cutting edge is nice and sharp. After honing, the tool should be ready for use!
Conclusion
If you’ve ever wondered what lathe tool inserts are for, Harbor Freight has the answer. Lathe tool inserts are used to hold cutting tools in place while machining. They’re available in a variety of sizes and shapes to fit your specific needs.