A table saw metal cutting blade is designed specifically for cutting metal materials with precision and accuracy. With its sharp teeth and durable construction, it ensures clean and efficient metal cutting tasks.
This type of blade is essential for professional and DIY metalworkers alike to achieve smooth and precise cuts in various types of metals, such as aluminum, steel, and copper. By using a table saw metal cutting blade, you can easily create accurate and clean cuts, making it an invaluable tool in metalworking projects.
Whether you are a professional or a hobbyist, having a high-quality table saw metal cutting blade is essential for achieving optimal results.
Achieving Precision And Power With The Right Blade Choice
Table of Contents
When it comes to achieving precision and power in metal cutting projects, choosing the right table saw metal cutting blade is crucial. The blade you use can have a significant impact on the quality of your cuts, as well as the safety of your work. In this section, we will discuss the factors you need to consider when choosing a table saw metal cutting blade, including blade material and construction, tooth count and design, blade size and compatibility. We will also address the common challenges faced when the wrong blade choice is made, such as poor cutting performance and accuracy, increased risk of kickback and accidents, and premature blade wear and tear.
Factors to consider when choosing a table saw metal cutting blade
When it comes to choosing a table saw metal cutting blade, several factors need to be taken into consideration:
- Blade material and construction
- Tooth count and design
- Blade size and compatibility
Blade material and construction
The material and construction of the table saw metal cutting blade can greatly affect its performance. Different blades are designed for specific types of metal cutting tasks, such as cutting aluminum, stainless steel, or mild steel. The most common blade materials include carbide-tipped, high-speed steel, and cermet. Each material has its own advantages and is suited for different applications.
Tooth count and design
The tooth count and design of the blade also play a crucial role in achieving precision and power. Blades with a higher tooth count are generally better suited for smoother cuts, while blades with a lower tooth count are ideal for faster cuts. Additionally, the tooth design can vary, with options like alternate top bevel (ATB) for clean cuts, triple-chip grind (TCG) for cutting tough materials, or flat-top grind (FTG) for ripping. Choosing the right tooth count and design depends on the type of metal being cut and the desired outcome.
Blade size and compatibility
Blade size and compatibility are important considerations to ensure the blade fits your table saw and can handle the cutting task at hand. It is crucial to check the manufacturer’s specifications and recommendations before purchasing a blade to avoid any compatibility issues. Using the correct blade size and ensuring compatibility will ensure optimal performance, safety, and longevity of both the blade and your table saw.
Common challenges faced with the wrong blade choice
Choosing the wrong table saw metal cutting blade can lead to various challenges and issues:
- Poor cutting performance and accuracy: Using the wrong blade can result in rough cuts, snagging, or even melting of the metal, leading to poor cutting performance and compromised accuracy.
- Increased risk of kickback and accidents: A blade that is not suitable for the specific metal cutting task can increase the risk of kickback, where the workpiece is violently thrown back towards the operator, causing accidents and injuries.
- Premature blade wear and tear: Using the wrong blade can cause premature wear and tear, resulting in a shorter lifespan of the blade. This can also lead to uneven wear, causing the blade to become dull faster and requiring more frequent replacements.
By considering factors such as blade material and construction, tooth count and design, and blade size and compatibility, you can ensure that you choose the right table saw metal cutting blade for your specific needs. Making the right choice will not only result in precise and powerful cuts but also enhance safety and prolong the life of your blade and table saw.
Choosing The Right Blade For Specific Metal Materials
Choosing the right blade for specific metal materials is crucial in achieving clean, precise cuts with your table saw. Different types of blades are designed to cut specific metal materials effectively and efficiently. In this article, we will explore the three main types of blades used for metal cutting: High-speed steel (HSS) blades, carbide-tipped blades, and diamond blades.
High-speed steel (HSS) blades
High-speed steel (HSS) blades are a popular choice for cutting non-ferrous metals like aluminum, brass, and copper. These blades are made from a hardened form of high-speed steel, which allows them to withstand the heat generated during cutting.
Advantages of HSS blades:
- HSS blades offer excellent durability and can withstand high temperatures, making them ideal for long cutting sessions.
- They are versatile and can be used for cutting both thin and thick metal sheets.
- HSS blades are cost-effective compared to other blade types.
Limitations of HSS blades:
- HSS blades are not suitable for cutting ferrous metals like steel or iron.
- When cutting non-ferrous metals, HSS blades can be prone to chip or dull over time.
Carbide-tipped blades
Carbide-tipped blades are specifically designed for cutting ferrous metals such as steel, iron, and stainless steel. These blades have carbide tips attached to their teeth, which greatly increases their cutting power and durability.
Benefits of using carbide-tipped blades:
- Carbide-tipped blades offer superior cutting performance and can handle even the toughest of metals.
- They have a longer lifespan compared to HSS blades, as carbide is harder and more resistant to wear.
- Carbide-tipped blades produce smoother cuts with less heat generated during the cutting process.
Diamond blades
Diamond blades are specialized blades designed for cutting hard metals such as cast iron, reinforced concrete, and other abrasive materials. These blades have small industrial-grade diamonds embedded in their cutting edge, allowing them to cut through the toughest metals with ease.
Applicability and advantages of diamond blades:
- Diamond blades are perfect for cutting hard metals that other blades may struggle with.
- They offer exceptional cutting speed and precision.
- Their diamond-infused design ensures minimal heat generation and extends their lifespan.
Choosing the right blade for your table saw is crucial in achieving accurate and efficient metal cutting results. Consider the type of metal material you are working with, and select a blade specifically designed for that material. Whether it’s HSS blades for non-ferrous metals, carbide-tipped blades for ferrous metals, or diamond blades for hard metals, having the right blade for the job will greatly enhance your cutting experience.
Extending The Lifespan And Performance Of Metal Cutting Blades
As a professional or hobbyist who frequently works with metal, you understand the importance of having a reliable and sharp cutting tool. A table saw metal cutting blade is an essential tool in your workshop, enabling precise and efficient cuts. To ensure that your blade performs at its best and lasts for a long time, it’s crucial to take proper care of it. In this section, we will discuss several maintenance techniques that can help you extend the lifespan and performance of your metal cutting blades.
Cleaning the Blade After Each Use
After every use, it’s crucial to clean your metal cutting blade to remove any accumulated gunk, debris, or other substances. Failure to clean the blade properly can lead to reduced performance and potentially cause damage. Here are some steps you can follow when cleaning your blade:
- Disconnect the table saw from the power source and remove the blade from the saw.
- Use a stiff bristle brush or an old toothbrush to remove the majority of the debris from the blade.
- Apply a cleaning solution specifically designed for cutting blades to help remove any stubborn residues. Make sure to follow the manufacturer’s instructions for the cleaning solution.
- Gently scrub the blade with a clean cloth or brush, ensuring all residue is adequately removed.
- Rinse the blade thoroughly with water to remove any remaining cleaning solution.
- Dry the blade completely before reattaching it to the table saw.
Removing Metal Shavings and Debris
In addition to cleaning the blade after each use, it’s crucial to remove any metal shavings or debris that may accumulate during the cutting process. This debris can cause friction, reduce cutting efficiency, and even lead to potential accidents. Here’s how you can remove metal shavings and debris from the blade:
- Ensure that the table saw is turned off and unplugged.
- Using a stiff brush or compressed air, gently remove the metal shavings and debris from the blade, paying attention to each tooth and gap.
- Inspect the blade for any remaining debris and remove it carefully to avoid injury.
Proper Methods for Cleaning and Drying
When cleaning your metal cutting blade, it’s important to use suitable methods to ensure you don’t damage the blade. Here are some tips for cleaning and drying your blade:
- Always use appropriate cleaning solutions specifically designed for cutting blades. Avoid using harsh chemicals or abrasive materials that could corrode or scratch the blade.
- Never soak the blade in water or any other liquid, as this can cause rust or corrosion.
- After cleaning, make sure to thoroughly dry the blade before storing or reusing it. Moisture left on the blade can lead to rust formation.
- Consider using a clean, lint-free cloth or air compressor to dry the blade effectively.
Sharpening and Honing Techniques for Dull Blades
Over time, even the highest quality metal cutting blades can become dull. When you notice a decrease in cutting performance or rough cuts, it’s a sign that your blade needs sharpening or honing. Here are some techniques you can use to restore the sharpness of your dull blades:
- Using a Blade Sharpener or Honing Guide
Investing in a blade sharpener or honing guide can be a worthwhile investment for maintaining your metal cutting blades. These tools help maintain the proper angle and provide consistent sharpening for each tooth of the blade. Follow the manufacturer’s instructions for the specific sharpener or honing guide you choose.
Recommended Sharpening Frequencies
The recommended frequency for sharpening your metal cutting blades can vary depending on usage. However, as a general guideline, it’s recommended to sharpen your blades after every 10 to 20 hours of use. This regular maintenance routine will help ensure optimal performance and prolong the lifespan of your blades.
Storing Blades Correctly to Prevent Damage
Proper storage is crucial to prevent damage to your metal cutting blades. Here are some tips to keep in mind:
- Avoid stacking multiple blades directly on top of each other to prevent them from banging together and potentially damaging the teeth.
- Consider using blade protectors or individual storage containers to keep your blades safe and organized.
- Store your blades in a dry, climate-controlled environment to avoid exposure to moisture and humidity.
By following these storage practices, you’ll help prevent rust, corrosion, and other types of damage that can occur when blades are improperly stored.
Avoiding Moisture and Humidity Exposure
Exposure to moisture and humidity can significantly impact the lifespan and performance of your metal cutting blades. It’s essential to store them in a dry environment and take precautions to avoid excessive exposure. Here are some steps you can take:
- Avoid leaving your blades exposed to humid conditions or places prone to moisture, such as basements or garages without proper climate control.
- Consider using moisture-absorbing packets or desiccants in the storage area to help absorb excess moisture.
- Regularly inspect your storage area for signs of moisture or water leaks and take appropriate actions to address any issues.
By keeping your blades away from moisture and humidity, you’ll help prevent rust, corrosion, and other forms of damage that can compromise their performance and lifespan.
Organizing Blades to Prevent Accidental Damage
Proper organization is essential not only for keeping your workspace tidy but also for preventing accidental damage to your metal cutting blades. Here are some tips to keep your blades organized:
- Use a dedicated storage system, such as a blade rack or wall-mounted holder, to keep your blades upright and secure.
- Ensure that the storage system you choose can accommodate the size and number of blades you have.
- Label each blade to easily identify the type and size, reducing the risk of accidentally using the wrong blade for a specific task.
By organizing your blades properly, you’ll minimize the chances of accidentally dropping or mishandling them, which can lead to damage or injuries.
Mastering The Art Of Table Saw Metal Cutting
When it comes to cutting metal with a table saw, proper technique and set-up are essential for achieving accurate and clean cuts. Whether you are a seasoned woodworker or a DIY enthusiast, mastering the art of table saw metal cutting requires a combination of skill, precision, and attention to detail. In this article, we will explore some key factors to consider when using a table saw for metal cutting and how to optimize your set-up for the best results.
Ensuring Proper Alignment and Setup of the Table Saw
Before diving into metal cutting, it is important to ensure that your table saw is properly aligned and set up. This includes checking the alignment of the blade and the parallelism of the fence. Improper alignment can lead to inaccurate cuts and potential safety hazards. To align the blade, use a reliable measurement tool such as a dial indicator to ensure the blade is perfectly parallel to the miter slot. Additionally, check the parallelism of the fence by measuring the distance from the blade to the fence at the front and back ends.
Checking Blade Parallelism and Fence Positioning
Blade parallelism and fence positioning are crucial for precise metal cutting. If the blade is not parallel to the miter slot, it can cause the material to bind or kickback during cutting. Use a straight edge or a specialized tool like a blade alignment jig to check and adjust the blade’s parallelism. Additionally, ensure that the fence is properly positioned parallel to the blade. This will allow for accurate and consistent cutting.
Utilizing Accurate Measurement Tools
Accurate measurements are essential for achieving precise cuts. Using reliable measurement tools such as calipers or a digital readout can help ensure that your cuts are spot on. Measure the thickness of the metal material you are working with and adjust the blade height accordingly. This will prevent excessive force on the blade, resulting in cleaner and safer cuts.
Maintaining Consistent Feed Rate and Pressure
Consistency is key when it comes to metal cutting. Maintaining a steady feed rate and applying consistent pressure throughout the cutting process will help you achieve cleaner and more controlled cuts. Avoid pushing the material too fast or applying excessive pressure, as this can cause the blade to bind or kickback. Take your time and let the blade do the work.
Controlling the Speed and Pressure During Cutting
Controlling the speed and pressure during cutting is essential for optimal results. Use a slower blade speed for thick or dense metals and a faster speed for thinner materials. Adjust the speed based on the type and thickness of the metal to achieve the desired cut quality. Additionally, be mindful of the pressure applied to the material. Applying too much force can lead to rough cuts or even damage the blade.
Avoiding Excessive Force on the Blade
Excessive force on the blade can result in damage or even breakage, posing a risk to your safety. Avoid forcing the material or overloading the blade. Let the blade cut at its own pace, applying steady pressure without putting excessive force on it. This will help prolong the life of the blade and ensure smooth cuts.
Implementing Safety Measures to Prevent Accidents
Safety should always be a priority when working with a table saw. To prevent accidents, follow these safety measures:
- Always wear appropriate protective equipment, including safety glasses, hearing protection, and gloves, when operating the table saw. This will safeguard you from potential injuries.
- Use push sticks and push blocks to keep your hands a safe distance from the blade while guiding the material through the cut. These tools provide better control and reduce the risk of accidents.
- Ensure the table saw is equipped with safety features such as a blade guard and a riving knife. These components help prevent kickback and protect against accidental contact with the blade.
- Regularly inspect the blade for any signs of damage or wear. Replace a worn-out blade to maintain optimal cutting performance and safety.
By implementing these safety measures, you can minimize the risk of accidents and create a safer working environment.
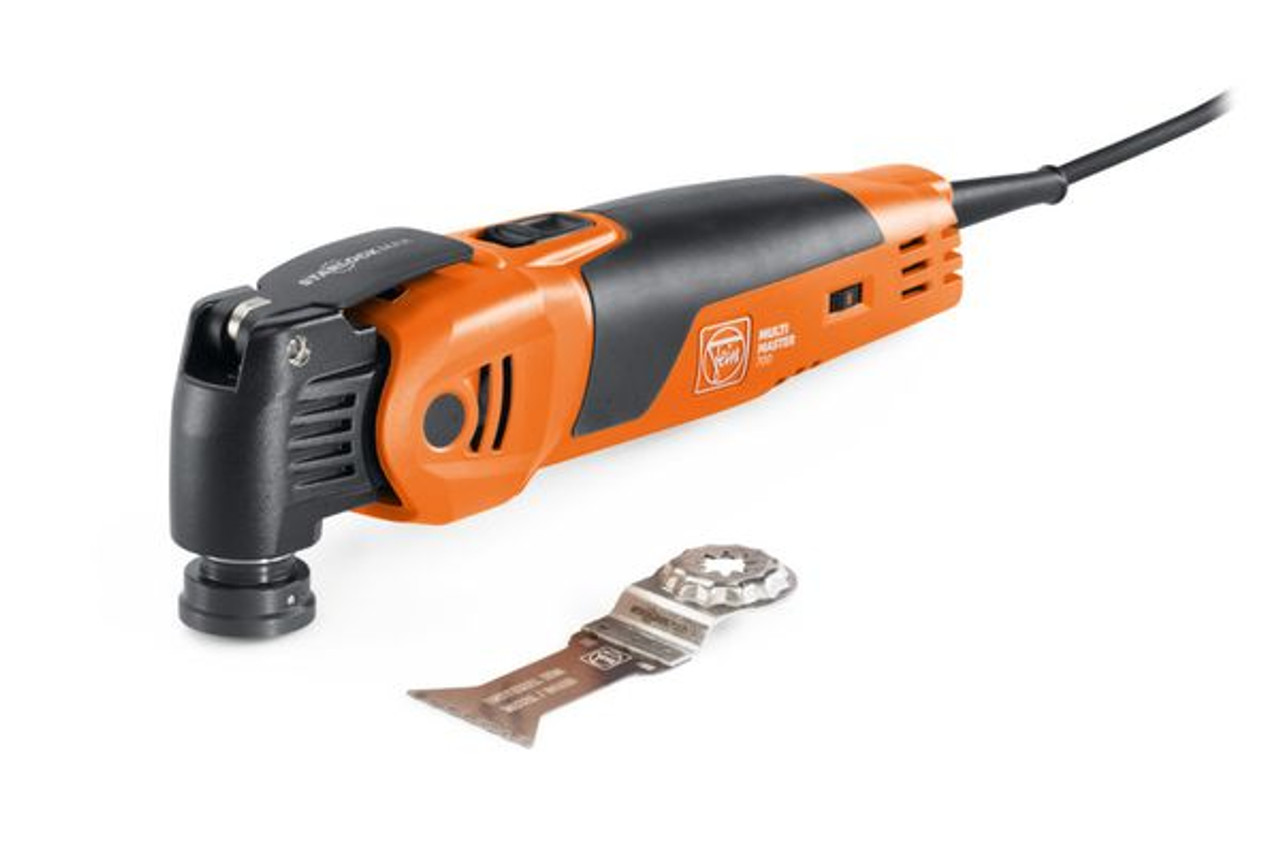
Credit: toolstoday.com
Frequently Asked Questions On Table Saw Metal Cutting Blade
Can You Put A Metal Cutting Blade On A Table Saw?
Yes, you can use a metal cutting blade on a table saw.
Can A Regular Table Saw Cut Metal?
Yes, a regular table saw can cut metal efficiently and accurately with the appropriate blade.
What Is The Best Blade For Cutting Metal?
The best blade for cutting metal is a carbide-tipped circular saw blade.
Can You Use A Wood Saw Blade To Cut Metal?
No, a wood saw blade should not be used to cut metal as it is not designed for that purpose.
Conclusion
To sum up, choosing the right table saw metal cutting blade is crucial for achieving precise and efficient results in your woodworking projects. By considering the key factors such as blade material, tooth count, and blade size, you can find the perfect blade for your specific needs.
Whether you are cutting through soft metals or tough alloys, investing in a high-quality blade will definitely enhance the performance of your table saw. Always remember to prioritize safety by wearing protective gear and following proper cutting techniques. Regular maintenance and blade sharpening will also ensure the longevity of your blade and the quality of your cuts.
Lastly, keep in mind the specific requirements of your projects and select the appropriate blade accordingly. So, go ahead and equip yourself with the right blade, and watch your table saw excel in cutting through metal with precision and ease.
- WoodRiver Plane reviews | Best Wood Hand Planer In 2024 - 19/10/2024
- The Best Tung Oil: The Ultimate Guide in 2024 - 19/10/2024
- 12 Inch Wood Planer: Smooth Your Woodworking Projects Like a Pro - 01/10/2023