Plasma cutting uses a mixture of gases, usually compressed air or oxygen, to create a plasma jet for cutting materials. Plasma cutting relies on ionization of the gas to generate the heat necessary to melt and cut through metal.
By using a focused beam of ionized gas, plasma cutting can achieve precise and efficient cuts in various types of materials. Plasma cutting is a widely used method for cutting through metal and other conductive materials. It offers many advantages, such as high precision, speed, and versatility.
The process involves the use of a plasma jet, which is created by a mixture of gases. This mixture typically consists of compressed air or oxygen, depending on the specific requirements of the cutting task. As the gas is ionized, it generates intense heat that can melt and sever the material being cut. This introduction provides an overview of plasma cutting and highlights the key role of gases in the process.
Understanding Plasma Cutting And Its Usage
Table of Contents
Plasma cutting relies on various gases, but the most commonly used gas is compressed air. It aids in creating a clean and precise cut by blowing away the molten metal. Other gases like oxygen or nitrogen may be used for different applications.
Plasma cutting is a highly efficient and widely used method of cutting metals. But have you ever wondered what gas is used for plasma cutting? In this blog post, we will delve into the world of plasma cutting, understanding its mechanism, importance, and applications.
Let’s get started!
How Plasma Cutting Works:
- Electric arc: An electric arc is formed between an electrode and the workpiece, creating an ionized gas known as plasma.
- Plasma generation: The arc superheats and ionizes the gas, turning it into a high-temperature plasma state.
- Focused jet: The plasma is forced through a small nozzle, which constricts its flow and creates a focused and powerful jet.
- Cutting action: This intense plasma jet cuts through the metal, melting and blowing away the molten material.
Importance And Applications Of Plasma Cutting:
- Versatility: Plasma cutting is versatile and can be used for cutting various types of metals, such as steel, stainless steel, aluminum, copper, and more.
- Speed and precision: It is known for its ability to make swift and precise cuts, making it ideal for industrial applications where accuracy is crucial.
- Efficiency: With plasma cutting, you can achieve high-quality cuts while minimizing material wastage, saving both time and cost.
- Industrial applications: Plasma cutting finds extensive use in industries like automotive, construction, fabrication, and metalworking. It is utilized for tasks like creating intricate designs, shaping metal components, and cutting thick sheets.
- Artistic applications: Plasma cutting’s precision and versatility also make it popular in the realm of artistic metalwork, enabling artists to create detailed sculptures, custom signs, and decorative pieces.
Plasma cutting is a powerful technique that harnesses the heat and precision of plasma to cut through various metals. Its efficiency, speed, and versatility have propelled it to become a vital tool in numerous industries. From industrial applications to artistic endeavors, plasma cutting continues to demonstrate its importance and contribute to advancements in metal fabrication.
Different Gases Used In Plasma Cutting
Plasma cutting utilizes various gases, including oxygen, air, nitrogen, and argon, to ensure optimal performance. These gases play a vital role in stabilizing the plasma arc and achieving precise and efficient cuts.
Plasma cutting is an efficient and versatile process used in various industries for cutting different types of metals. One of the key components in achieving a clean, precise cut is the gas used in the plasma cutting process. Let’s take a closer look at the characteristics, benefits, and suitable applications of three commonly used gases in plasma cutting.
Argon Gas
- Argon is an inert gas commonly used in plasma cutting due to its non-reactive nature.
- It is particularly beneficial when working with metals that are sensitive to oxidation, as argon prevents the formation of an oxide layer.
- Argon gas ensures a smooth and clean cut without any discoloration or distortion, resulting in high-quality finished products.
- Suitable applications for argon gas in plasma cutting include stainless steel, aluminum, copper, and titanium.
Nitrogen Gas
- Nitrogen gas is another commonly used gas in plasma cutting, known for its affordability and availability.
- Its primary advantage is that it does not react with most metals, making it ideal for applications where oxidation could negatively impact the cut quality.
- When used in plasma cutting, nitrogen gas provides a clean and precise cut with minimal dross formation, reducing the need for post-cutting operations.
- Nitrogen gas is suitable for cutting stainless steel, carbon steel, and aluminum.
Oxygen Gas
- Oxygen gas is often used for its excellent cutting capabilities and affordability.
- It reacts with the metal being cut, resulting in an exothermic reaction that enhances the cutting process, particularly for carbon steel.
- When combined with a plasma cutting system, oxygen gas produces fast and efficient cuts, making it the go-to choice for thicker materials.
- Oxygen gas is commonly used in applications involving carbon steel, mild steel, and cast iron.
By understanding the characteristics, benefits, and suitable applications of different gases used in plasma cutting, you can make informed decisions to optimize your cutting process for specific materials and achieve exceptional results.
Factors To Consider When Choosing Gas For Plasma Cutting
Choosing the right gas for plasma cutting requires considering factors like cutting speed, material thickness, and desired edge quality. Different gases, such as nitrogen, oxygen, and argon/hydrogen mixtures, offer specific advantages depending on the application.
Plasma cutting is a versatile and efficient method for cutting various materials. However, the choice of gas used in plasma cutting plays a crucial role in achieving optimal results. Here are some factors to consider when selecting the appropriate gas for your plasma cutting needs:
Material Type And Thickness
Different materials require specific gases to achieve optimal cuts. Consider the following factors when selecting gas based on the material type and thickness:
- Material compatibility: Ensure the gas you choose is suitable for the material you are cutting. For example, oxygen is commonly used for carbon steel, while nitrogen or argon-hydrogen mixtures are ideal for stainless steel.
- Oxidation concerns: Some materials, such as aluminum, are prone to oxidation during the cutting process. Choosing gases like nitrogen or argon-hydrogen mixtures can prevent this issue and maintain clean cuts.
- Thermal conductivity: The thermal conductivity of the gas affects the cutting efficiency. Higher thermal conductivity gases like hydrogen or nitrogen can improve cutting speed and quality, especially for thicker materials.
- Material thickness: Thicker materials require gases with higher heat capacity and faster heat dissipation. Opt for gases with superior thermal properties to ensure smooth and precise cuts.
Desired Cut Quality
The quality of the cut is crucial for many applications. Consider the following factors when selecting gas based on desired cut quality:
- Cleanliness of cuts: Different gases produce varying levels of dross and cleanliness during the cutting process. Nitrogen, for instance, provides clean cuts with minimal dross, while oxygen may result in more dross.
- Smoothness and precision: Gases with good arc stability and high-quality plasma enable smoother and more precise cuts. Choosing gases with lower arc voltage and better plasma quality can improve overall cut quality.
- Beveling requirements: If your cutting project involves beveling, choose gases that allow for better beveling control. Certain gas mixtures can help achieve desired bevel angles and minimize bevel defects.
Cost And Availability Of Gas
While considering gas options for plasma cutting, it’s essential to keep in mind the cost and availability factors:
- Gas cost: The cost of gas can significantly impact your overall cutting expenses. Compare the prices of different gases and evaluate their cost-effectiveness based on your cutting requirements.
- Gas availability: Ensure that the chosen gas is readily available in your area. Consider the gas supply chain and availability from local suppliers to avoid any production delays or additional logistical challenges.
Considering these factors will help you make an informed decision when selecting the appropriate gas for your plasma cutting needs. Remember to prioritize material compatibility, desired cut quality, and cost-effectiveness to achieve optimal results in your cutting projects.
Safety Precautions And Best Practices
Plasma cutting requires the use of a specific gas to ensure safety and efficiency. The most commonly used gas for plasma cutting is compressed air, although other gases such as oxygen or nitrogen can be used depending on the material being cut.
Employing the right gas is vital to achieve clean and precise cuts.
Plasma cutting, an effective method for metal fabrication, utilizes a combination of high-temperature ionized gas and electrical currents to slice through various materials. To ensure safe and efficient plasma cutting, it is crucial to adhere to proper safety precautions and best practices.
This section will outline essential measures, including proper ventilation and extraction systems, regular equipment maintenance, and the use of personal protective equipment (PPE).
Proper Ventilation And Extraction Systems:
To mitigate the potential hazards associated with plasma cutting, adequate ventilation and extraction systems are indispensable. Here are important points to consider:
- Ventilation: Establish well-ventilated areas in your workspace to minimize air contamination from fumes and gases produced during plasma cutting. This can be achieved through good airflow and ventilation systems, such as open windows or mechanical ventilation.
- Extraction Systems: Employ local exhaust ventilation (LEV) systems designed specifically for plasma cutting. These systems remove contaminants directly at the source, efficiently capturing and filtering hazardous fumes generated during the process.
- Positioning: Position the extraction systems as close as possible to the cutting operation. By doing so, you can optimize the collection and removal of the harmful byproducts generated, ensuring a cleaner and safer work environment.
Regular Equipment Maintenance:
Performing regular maintenance on your plasma cutting equipment is paramount to ensure safe operation, longevity, and optimal performance. Consider the following:
- Inspections: Conduct regular inspections of your plasma cutter to identify any signs of wear, damage, or malfunctions. Prioritize checks on cables, torch components, and connections to guarantee their integrity.
- Cleaning: Thoroughly clean the torch and cutting surface before each session to remove any debris or accumulated residue. Proper cleaning not only enhances cutting quality but also helps prevent potential hazards.
- Component Replacement: Replace worn-out or damaged parts promptly to maintain the efficiency and reliability of your plasma cutting equipment. Consult the manufacturer’s guidelines for recommended replacement intervals and procedures.
Personal Protective Equipment (Ppe):
To safeguard yourself from potential hazards associated with plasma cutting, donning appropriate personal protective equipment (PPE) is imperative. Take note of these key considerations:
- Eye Protection: Wear safety glasses or a face shield equipped with a shade rating appropriate for plasma cutting. These protective measures shield your eyes from harmful radiation and potential metal splatters.
- Protective Clothing: Utilize flame-resistant clothing, gloves, and aprons to shield your body from sparks, hot metal, and potential fire hazards. These protective garments should fit snugly to minimize the possibility of catching onto any moving parts.
- Respiratory Protection: Depending on the materials being cut and your workspace conditions, utilize respirators or dust masks specifically designed for plasma cutting. These filters aid in preventing inhalation of hazardous fumes and airborne particles.
By adhering to proper ventilation and extraction systems, prioritizing regular equipment maintenance, and donning appropriate personal protective equipment (PPE), you can ensure a safer plasma cutting environment. Always prioritize safety to maximize productivity and minimize potential risks.
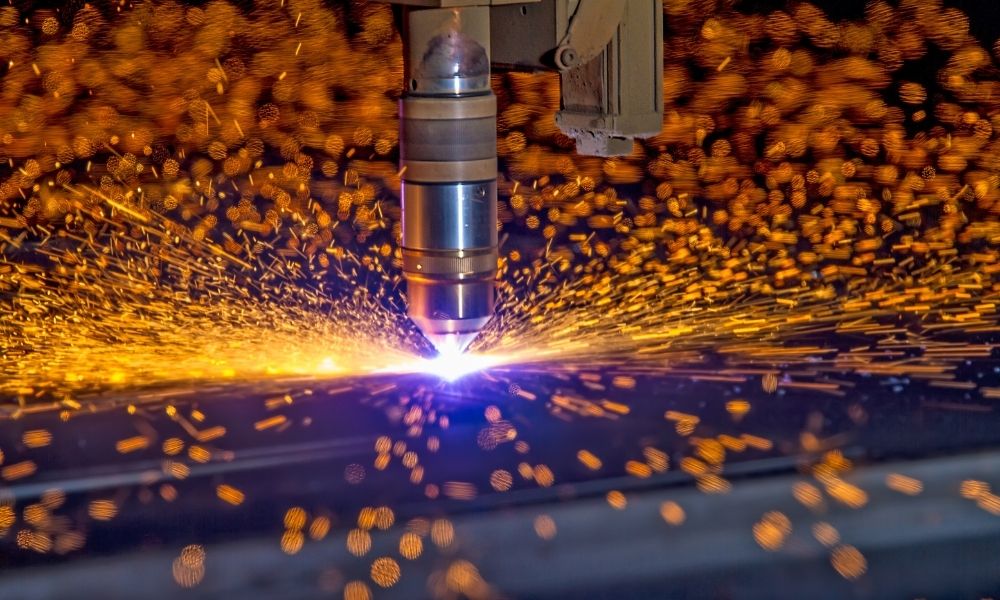
Credit: www.mac-tech.com
Frequently Asked Questions For What Gas Is Used For Plasma Cutting
What Is The Best Gas For Plasma Cutting?
The best gas for plasma cutting is usually compressed air.
Can You Use Co2 For Plasma Cutting?
Yes, CO2 can be used for plasma cutting.
What Two Types Of Gases Can Be Used For Plasma Arc Cutting?
Two gases commonly used for plasma arc cutting are nitrogen and oxygen.
What Gases Can Be Used For Plasma?
Gases like argon, helium, hydrogen, nitrogen, and oxygen can be used for plasma.
Conclusion
The choice of gas utilized in plasma cutting plays a crucial role in the efficiency and effectiveness of the process. Different gases, such as oxygen, nitrogen, argon, and a mixture of these, have distinct properties that cater to varying cutting needs.
Oxygen is typically used for mild steel, while nitrogen provides clean cuts on stainless steel and aluminum. Argon, on the other hand, is employed for non-metallic materials. The gas selection for plasma cutting depends on factors like the material being cut, the desired quality of the cut, and the thickness of the material.
By understanding the characteristics of each gas and tailoring it to the specific requirements, plasma cutting operators can achieve precise and high-quality results. It’s essential to consult professionals in the field who can provide guidance on selecting the appropriate gas to optimize your plasma cutting operations.
- WoodRiver Plane reviews | Best Wood Hand Planer In 2024 - 19/10/2024
- The Best Tung Oil: The Ultimate Guide in 2024 - 19/10/2024
- 12 Inch Wood Planer: Smooth Your Woodworking Projects Like a Pro - 01/10/2023